Understanding the Role of Injection Mould Companies in Modern Manufacturing
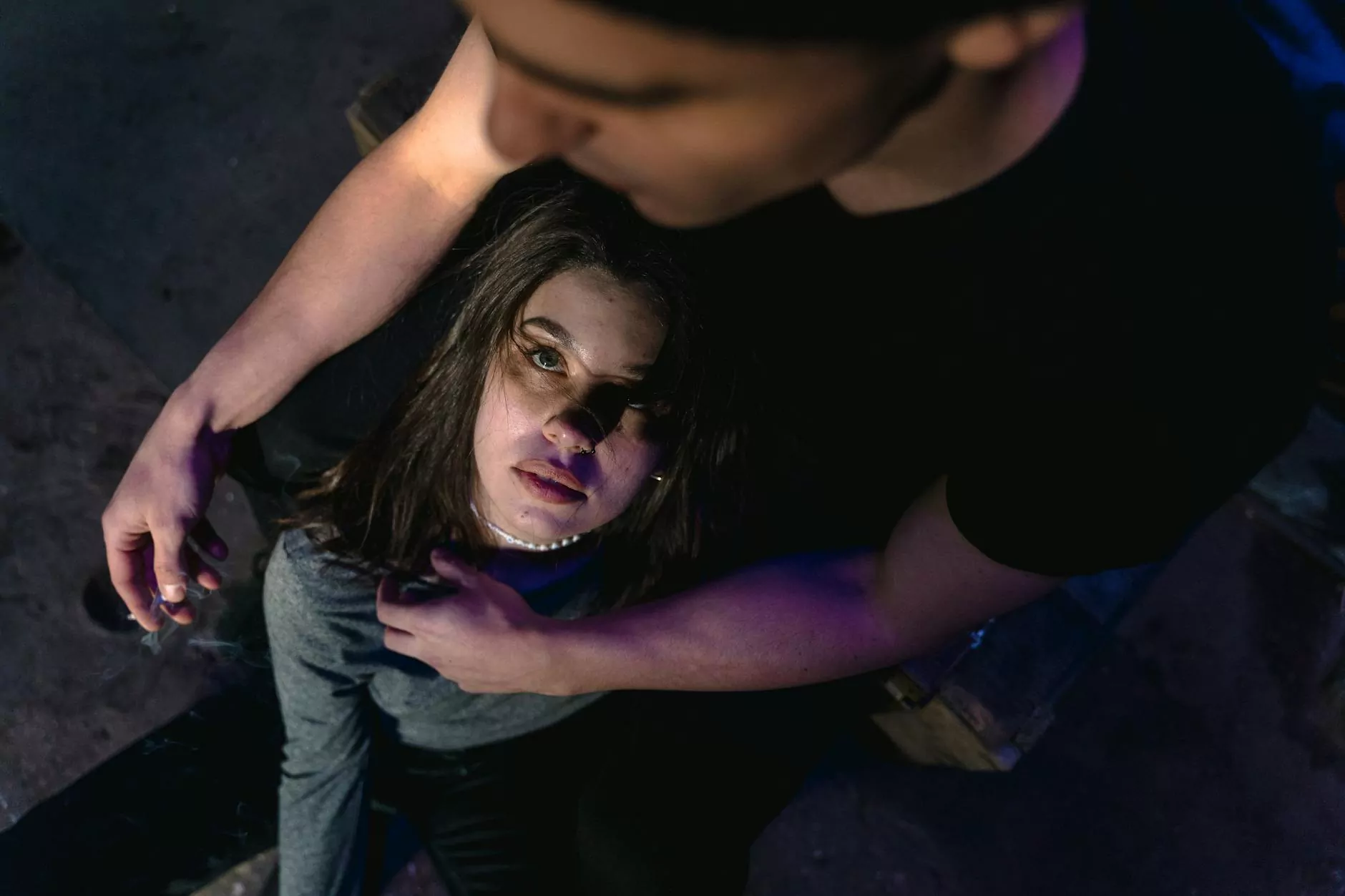
In today's fast-paced industrial landscape, injection mould companies are at the forefront of manufacturing innovation. These companies specialize in creating precision parts and complex designs with efficiency and excellence. This article will delve into the world of injection moulding, exploring the processes involved, the advantages of working with experienced moulding companies, and their significant contributions to various industries.
The Basics of Injection Moulding
Injection moulding is a highly efficient manufacturing process used to produce a wide variety of parts by injecting molten material into a mould. This technique is particularly popular for its versatility and ability to create intricate designs that would be difficult to achieve through other manufacturing methods.
How Injection Moulding Works
The injection moulding process typically involves the following steps:
- Material Selection: Choosing the right material is critical, as it affects the part's properties and performance.
- Designing the Mould: Engineers design a precise mould that will form the final product, ensuring all specifications are met.
- Heating the Material: The chosen material, often thermoplastic, is heated until it becomes molten and can be easily injected.
- Injection: The molten material is injected into the mould under high pressure.
- Cooling: After injection, the material cools and solidifies, taking the shape of the mould.
- Demoulding: Once cooled, the mould opens, and the finished part is ejected.
Quality and Precision in Manufacturing
Injection mould companies prioritize high-quality standards in their manufacturing processes. This ensures that each part produced meets the demands of strict industry specifications. Utilizing advanced technology and skilled workforce enables these companies to deliver precision-engineered products that maintain dimensional accuracy and consistency.
Benefits of Engaging with Injection Mould Companies
Partnering with dedicated injection mould companies brings many advantages:
- Cost-Efficiency: Bulk production brings down unit costs, making it a financially viable option for manufacturers.
- Versatility: A wide range of materials can be used, including plastics, metals, and composites, allowing for various applications.
- Scalability: Moulding processes are easily scalable, making it seamless to expand production as demand increases.
- Rapid Prototyping: Companies can create prototypes quickly, allowing for faster product development cycles.
- Minimized Waste: The process is designed to maximize material usage and minimize waste, contributing to sustainable practices.
Industries Benefiting from Injection Moulding
Many sectors benefit immensely from the capabilities of injection mould companies. These industries rely on precision parts for functionality and efficiency:
1. Automotive Industry
The automotive industry utilizes injection moulding for producing intricate parts such as dashboard components, gears, and body panels. This technique ensures that parts are lightweight yet durable, contributing to better fuel efficiency.
2. Consumer Electronics
In the realm of consumer electronics, manufacturers depend on injection moulding for creating housings, connectors, and internal components. The precision offered by moulding is ideal for the compact designs required in modern devices.
3. Medical Devices
Healthcare products, such as syringes, surgical instruments, and diagnostic equipment, rely on the high standards of hygiene and accuracy that injection moulding provides. The ability to produce complex shapes ensures functional and safe devices.
4. Packaging
Injection moulding plays a crucial role in producing packaging solutions that require strong, lightweight materials. From bottle caps to containers, this method ensures that products are both appealing and functional.
5. Construction
In construction, modular components created through injection moulding can enhance building efficiency and sustainability. Parts like window frames and fittings can be produced with great precision and strength.
Choosing the Right Injection Mould Company
When selecting an injection mould company, several factors should be taken into consideration to ensure you choose a partner that meets your manufacturing needs:
1. Experience and Expertise
Look for companies with a strong track record in the industry. An experienced company will have a wealth of knowledge that can contribute to successful project outcomes.
2. Technology and Equipment
The type of machinery and technology used is critical. Companies with modern equipment can produce higher-quality parts faster and more efficiently, which can significantly benefit your operations.
3. Quality Assurance Processes
Ensure that the company has stringent quality control measures in place. Certifications such as ISO 9001 can be a good indicator of their commitment to quality.
4. Customization Options
Every project is unique, and a good injection mould company should offer customization to cater to your specific requirements. This might include bespoke mould designs or material selections.
5. Customer Service
Responsive and knowledgeable customer service is vital for effective communication throughout the project lifecycle. A supportive partner will help navigate any issues that may arise.
Future Trends in Injection Moulding
The future of injection mould companies looks promising, with several emerging trends shaping the industry. Understanding these trends is essential for staying competitive:
1. Sustainability Initiatives
With growing environmental awareness, many companies are looking to adopt sustainable practices. This includes the use of biodegradable materials and energy-efficient production processes.
2. Advanced Materials
Innovations in material science are leading to new possibilities in injection moulding. High-performance polymers and composites are enhancing product capabilities and performance.
3. Smart Manufacturing
The integration of IoT (Internet of Things) in manufacturing processes enables real-time monitoring and data analytics, leading to improved efficiency and reduced downtime.
4. Automation and Robotics
Automation is revolutionizing the injection moulding process, increasing production speed and consistency while reducing labor costs.
Conclusion
In conclusion, injection mould companies are integral to modern manufacturing, providing innovative solutions across diverse industries. Their ability to deliver quality, precision, and efficiency makes them invaluable partners in product development. As technology advances, these companies will continue to evolve, driving further changes in manufacturing practices and enhancing product capabilities.
If you are considering partnering with an injection moulding company for your next project, look no further than Deep Mould. With expertise in metal fabrication and a commitment to excellence, they are poised to meet all your manufacturing needs.