Understanding Injection Moulding Tools: A Comprehensive Guide
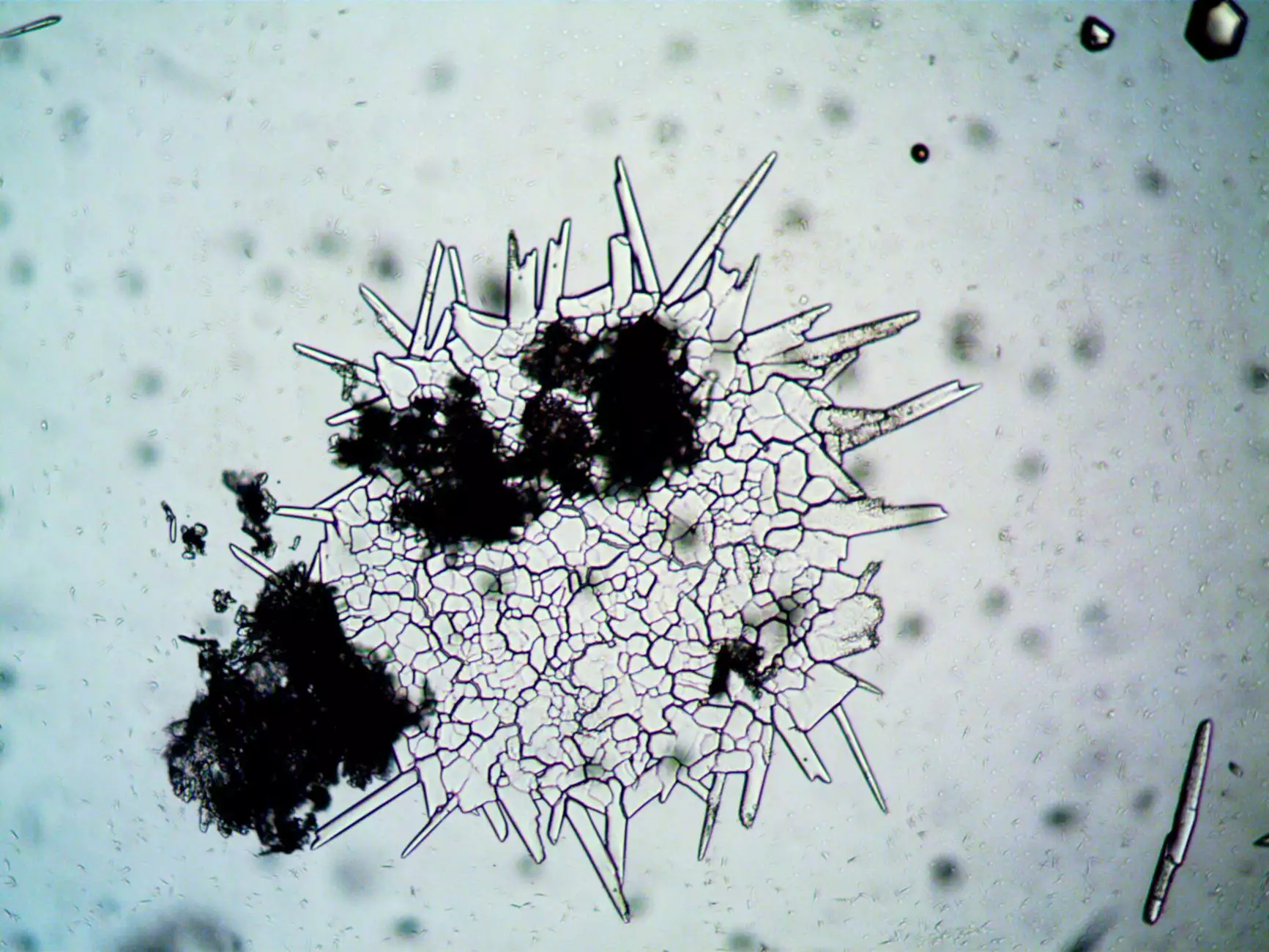
Injection moulding tools play a crucial role in the manufacturing industry, particularly for businesses involved in metal fabrication. They are designed to create parts and products through a process that involves injecting molten material into a mould. This comprehensive guide will delve into various aspects of injection moulding tools, including their types, applications, benefits, and how selecting the right provider can enhance the production process, especially for businesses like Deepmould.net.
What Are Injection Moulding Tools?
Injection moulding tools are special equipment used for the injection moulding process, a method that involves shaping materials such as plastics or metals by injecting them into a mould. The mould is designed to provide the exact shape and dimensions of the final product. This process is widely used in various industries, including automotive, electronics, consumer products, and more.
The Components of Injection Moulding Tools
Understanding the components of injection moulding tools is essential for any business looking to invest in this technology. Here are the key parts:
- Mould Base: The structure that holds the mould cavity and core.
- Mould Cavity: The part of the mould that shapes the material into the desired form.
- Mould Core: Works in conjunction with the cavity, determining the internal features of the part.
- Injection Unit: The mechanism that heats and injects the molten material into the mould.
- Clamping Unit: Holds the mould shut during injection and ensures that it remains closed while molten material is injected.
Types of Injection Moulding Tools
There are various types of injection moulding tools, each suitable for different materials and production needs. Here are the most common types:
1. Single Cavity Mould
This type of mould produces one part at a time. It is often used for low-volume production runs where precision is paramount.
2. Multi-Cavity Mould
A multi-cavity mould can produce multiple parts simultaneously. This is more efficient for high-volume production, reducing cycle time and cost per part.
3. Hot Runner Mould
In a hot runner system, the plastic remains molten in the runner system, allowing for faster cycle times and less waste. However, it requires higher initial investment and maintenance.
4. Cold Runner Mould
This system relies on solidified plastic in the runner once the mould is opened. Although it has a lower initial cost, it produces more waste due to the runner material that must be reprocessed.
Applications of Injection Moulding Tools
The versatility of injection moulding tools allows them to be used in various applications across multiple industries:
- Automotive Industry: Used to create parts such as dashboards, panels, and other components.
- Consumer Goods: From toys to household items, injection moulding is vital for mass production.
- Medical Devices: Ensures precise and sterile parts for life-saving medical equipment.
- Electronics: Produces components like casings and connectors in large volumes with high accuracy.
Benefits of Using Injection Moulding Tools
Investing in injection moulding tools offers several advantages:
1. High Efficiency and Speed
The injection moulding process is incredibly efficient, allowing for rapid production cycles, which is essential for meeting market demand.
2. Cost-Effectiveness
While the initial setup cost can be high, the cost per part decreases significantly with high volume production, making it economically viable.
3. High Precision and Consistency
These tools ensure that every part produced is identical in terms of dimensions and quality, which is crucial in fields such as automotive and aerospace.
4. Flexibility in Design
Injection moulding tools allow for complex geometries and designs that might not be achievable with other manufacturing processes.
Choosing the Right Injection Moulding Tools Provider
For businesses in the metal fabrication sector, selecting the right provider for injection moulding tools is crucial. Deepmould.net stands out for several reasons:
1. Industry Experience
With years of experience in the field, Deepmould.net has a rich portfolio and deep understanding of the needs of metal fabricators.
2. Quality Assurance
Deepmould.net implements strict quality control measures to ensure that their moulds meet international standards.
3. Customized Solutions
Every business is unique, and Deepmould.net offers tailored solutions that align with your specific production requirements.
4. Advanced Technology
Investing in the latest technology allows Deepmould.net to provide precision tools that enhance production efficiency.
Conclusion
In conclusion, injection moulding tools are a foundational element in the manufacturing sector that offers unparalleled efficiency, precision, and versatility. Understanding their components, types, applications, and the benefits they provide is essential for any business in the metal fabrication industry. By choosing a reliable provider like Deepmould.net, your business can harness the full potential of these tools to enhance product offerings while reducing costs and improving production timelines.
As the manufacturing landscape continues to evolve, the value of high-quality injection moulding tools cannot be overstated. Make informed decisions and invest in the future of your business today.