The Dynamic World of China Die Casting Factories
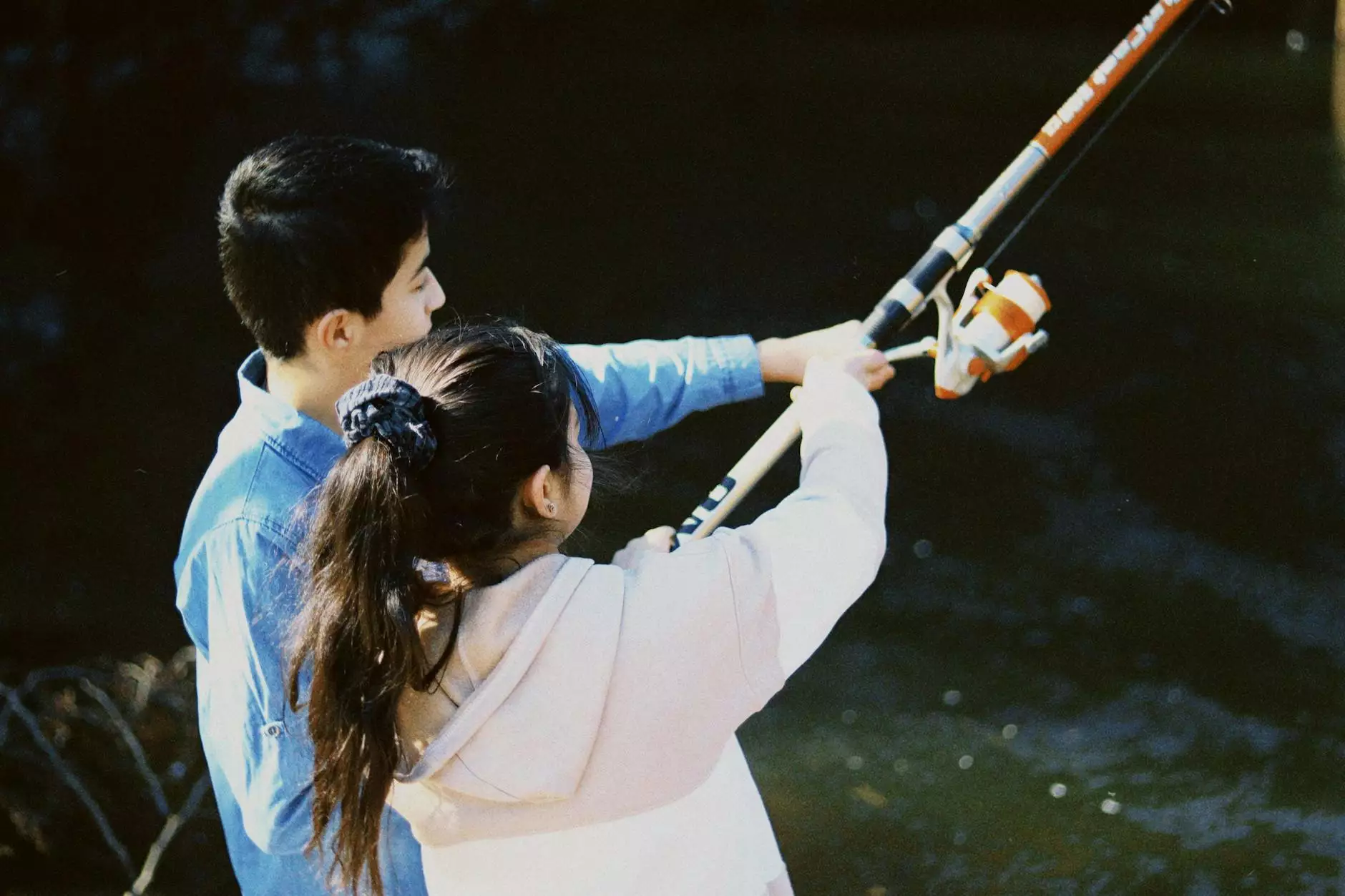
China die casting factories stand at the forefront of today's manufacturing revolution, showcasing innovation, precision, and efficiency. In this article, we delve deep into the fascinating realm of die casting in China, emphasizing the techniques, technologies, and industries that benefit from this crucial manufacturing process.
Understanding Die Casting: A Brief Overview
Die casting is a manufacturing process that involves forcing molten metal into a mold cavity under high pressure. This process is extensively used for creating complex shapes in a variety of materials, primarily non-ferrous metals such as aluminum, zinc, and magnesium.
- Precision: Die casting is revered for producing high-precision components that require minimal finishing work.
- Speed: The process is rapid, enabling the production of large volumes in a short period.
- Complexity: It allows for intricate designs that would be difficult or too costly to achieve using other manufacturing methods.
Why Choose a China Die Casting Factory?
With the global manufacturing landscape continuously evolving, China's die casting facilities have emerged as a key player. Here are several compelling reasons why businesses worldwide prefer to work with China die casting factories.
1. Advanced Technology and Innovation
Chinese die casting factories leverage cutting-edge technology and state-of-the-art machinery. This commitment to innovation enhances quality and efficiency while reducing costs. Significant investments in modern equipment, like robotic arms and AI-driven quality control systems, ensure that production is not only faster but also more reliable.
2. Cost Efficiency
Cost factors heavily influence manufacturing decisions. China's factories are known for their ability to provide competitive pricing without compromising quality. This cost efficiency allows companies to maximize their profits while delivering quality products to their customers.
3. Skilled Workforce
The workforce in China die casting factories is trained rigorously, ensuring high standards are maintained throughout the production process. Skilled technicians manage complex machinery, ensuring each component is produced with the utmost precision.
4. Comprehensive Supply Chains
China boasts an extensive supply chain network, enabling quick access to raw materials and components. This logistical advantage allows die casting manufacturers to streamline operations, significantly reducing lead times.
Key Industries Benefiting from Die Casting in China
The applications of die casting are numerous and span across various industries. Here are some of the key sectors that benefit significantly from the expertise found in China die casting factories:
- Automotive: The automotive industry requires high-strength, lightweight components that can withstand extreme conditions.
- Electronics: Die casting is fundamental in manufacturing parts for consumer electronics, ensuring functionality and durability.
- Aerospace: The aerospace sector relies on precise and reliable components for safety and performance.
- Medical: Medical devices and equipment often demand the highest standards of precision, with die casting meeting these stringent requirements.
The Die Casting Process Explained
To appreciate the majesty of China die casting factories, it's essential to understand the die casting process itself. Here’s a step-by-step breakdown:
1. Mold Creation
The first stage involves constructing a die, which is typically made from steel or iron. This mold has the shape of the desired component and must withstand repeated high-pressure injections of molten metal.
2. Melting the Metal
Next, the metal is melted in a furnace, reaching temperatures depending on the material being used (e.g., aluminum melts around 660 degrees Celsius).
3. Injection
Molten metal is then injected into the mold at high pressures (typically between 1,000 to 30,000 psi), filling the cavities to ensure precise replication of the mold.
4. Cooling
After the metal fills the mold, it is cooled, allowing it to solidify. Cooling times vary based on the thickness and type of metal.
5. Ejection
Once cooled, the die is opened, and the newly formed part is ejected, ready for subsequent finishing processes.
Quality Control in China Die Casting Factories
Quality control is paramount in die casting, especially in high-stakes industries like automotive and aerospace. China die casting factories implement rigorous quality assurance protocols, including:
- Visual Inspections: Excessive defects are often caught during visual inspections before parts are sent for further processing.
- Dimensional Checks: Components are frequently measured to ensure they meet the specified tolerances and dimensions.
- Material Testing: Samples are often tested for durability, strength, and other physical properties to guarantee product integrity.
Sustainability Efforts in Die Casting
With increasing global emphasis on sustainability, many China die casting factories are adopting eco-friendly practices. These practices include:
- Recycling Metal: Many factories recycle scrap metal, reducing waste and conserving natural resources.
- Energy Efficiency: Factories are implementing energy-efficient technologies and processes to minimize their carbon footprint.
- Water Conservation: Innovative cooling solutions have been developed to use less water during the die casting process.
Choosing the Right China Die Casting Factory
Selecting the right manufacturing partner is critical for business success. Here are some factors to consider when choosing a China die casting factory:
1. Experience and Reputation
Look for factories with a proven track record in the industry. Reading customer reviews and seeking recommendations can help gauge a factory's reliability and expertise.
2. Certifications
ISO certifications and quality assurances indicate a factory's commitment to maintaining high manufacturing standards. Ensure that the factory adheres to international quality management systems.
3. Communication
Effective communication is essential for successful partnerships. Choose a factory that is responsive and transparent in their dealings.
4. Capabilities
Assess the factory's production capabilities, including the range of materials they can work with and their capacity to meet your volume requirements.
Future Trends in Die Casting
The die casting industry is steadily evolving. Several trends are shaping the future of China die casting factories:
- Adoption of 3D Printing: 3D printing technology is beginning to revolutionize how molds are created, making the process even more efficient.
- Increased Automation: More factories are integrating automated systems to enhance productivity and reduce labor costs.
- Focus on Green Technologies: Research and development efforts are underway to minimize environmental impacts further.
Conclusion: Embracing the Potential of Die Casting in China
In conclusion, China die casting factories play a vital role in the global manufacturing landscape. Their commitment to quality, pioneering technology, and sustainability efforts make them a valuable partner for various industries worldwide. By understanding the intricacies of die casting, businesses can leverage these manufacturing capabilities to enhance their product offerings and remain competitive in an ever-evolving market.
Choosing the right factory, recognizing the advantages, and staying abreast of the trends will ensure that companies maximize their potential in the die casting arena.